Be a Part of the Plastics Reformation
Consumers are aware of the problematic environmental issues associated with traditional petroleum-based plastic. It’s driving the increased demand globally for sustainable biobased and biodegradable plastics.
Maybe you’ve tried your hand at bioplastics, and it just didn’t work out. Green Dot has spent a decade perfecting bioplastics, and is ready to work with you to ensure you’re a part of this growth — instead of being left behind by it.
By now, you’ve had customers come to you looking for a sustainable alternative and if not, they will sooner rather than later. Green Dot bioplastic materials can seamlessly replace traditional plastics such as polyethylene, polypropylene, nylon, and ABS to name a few. You can sample our bioplastics to make sure they work with your equipment, meet your expectations and match your tolerances.
Your customers are demanding that green alternatives — be it products or packaging made from renewable resources — be biobased, biodegradable or compostable and provide a number of other environmental benefits.
You Can Offer Sustainable Plastic
When you partner with Green Dot, you can offer innovative bioplastics to your customers. Our raw materials can be used to make just about anything you can imagine, while lowering the environmental impact, decreasing the dependency on petroleum-based plastics and using reclaimed products before they are discarded.
Products made by injection molders with Green Dot bioplastics:
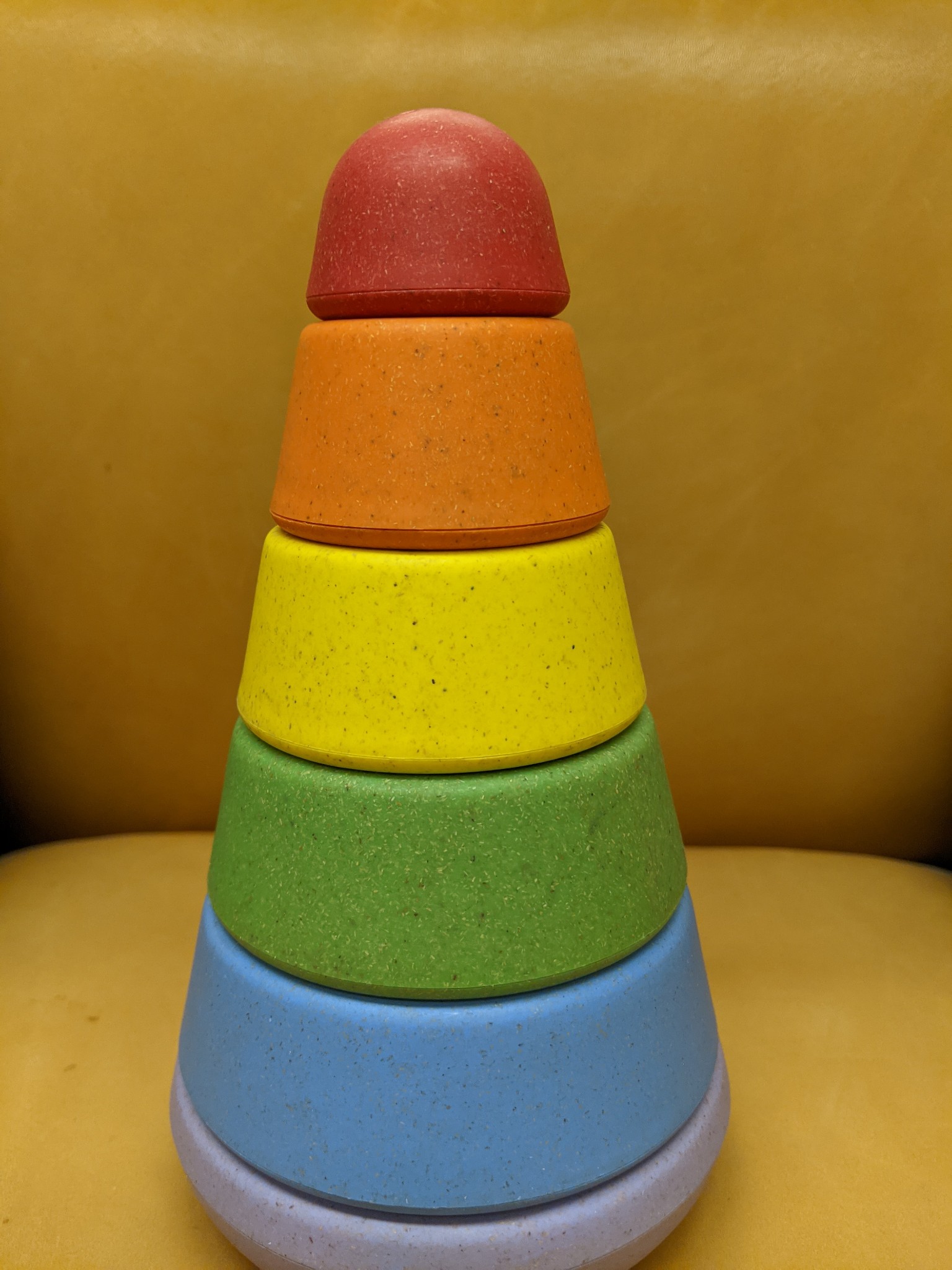
Wood-plastic Composites
Provide the look of wood and get the design flexibility of plastic
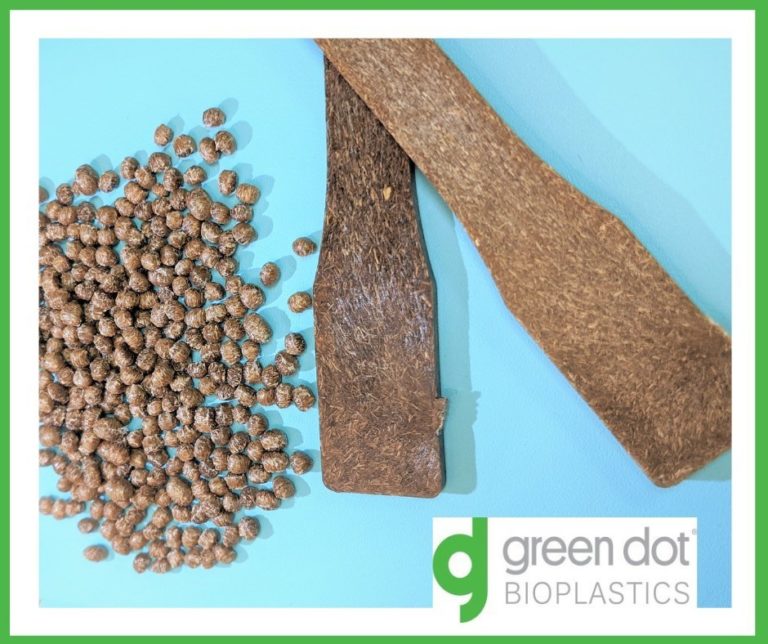
Natural Fiber Reinforced Plastic Composites
Lighter, quieter, and have a more sustainable life-cycle
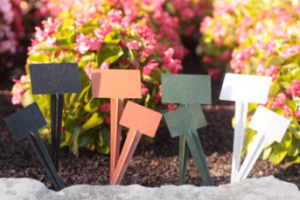
Biocomposites
Organic fillers, such as corn cob, reduce the non-renewable feedstock and perform
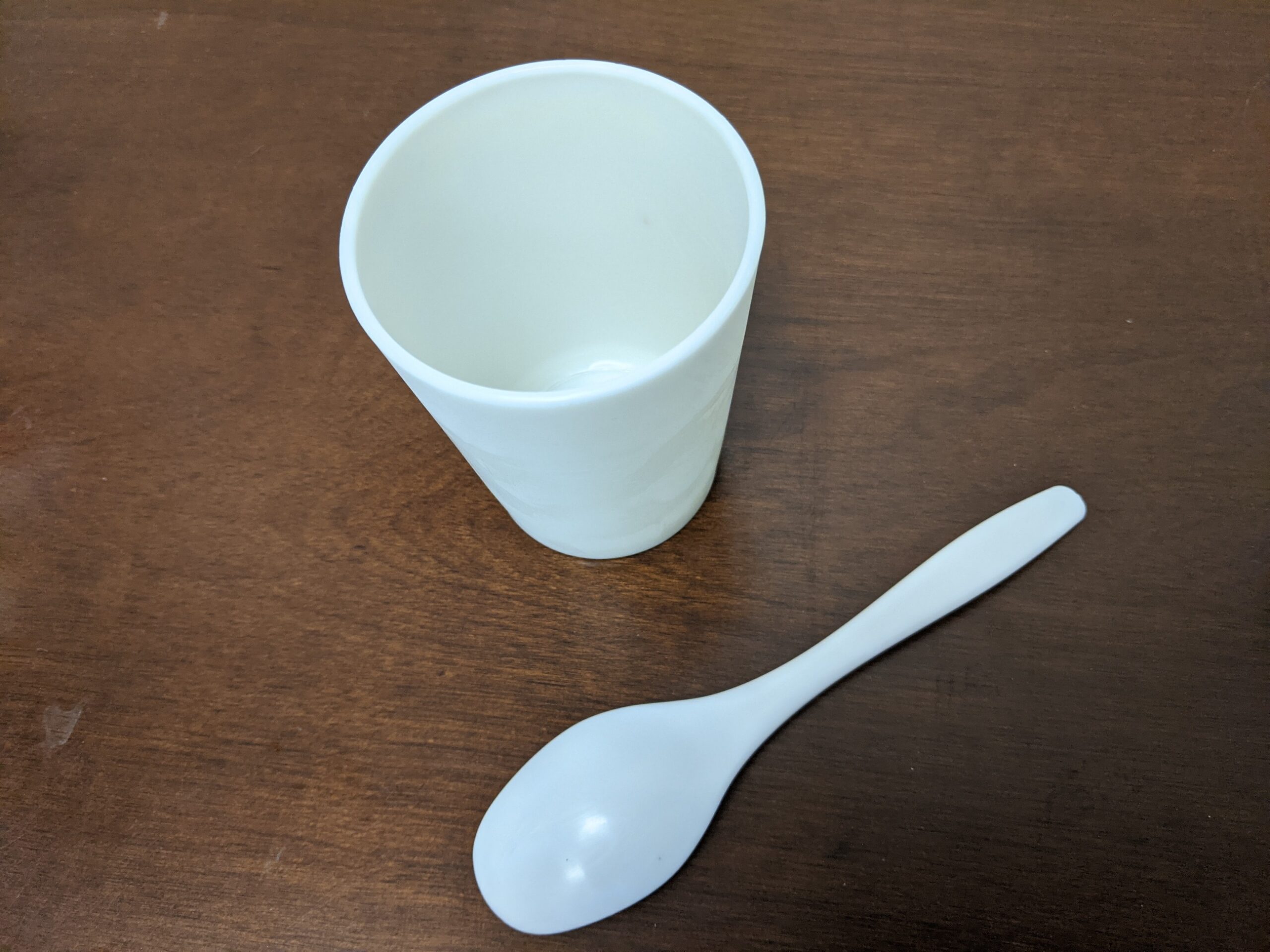
Biodegradables
Reduce the pollution and waste of single-use and disposable products
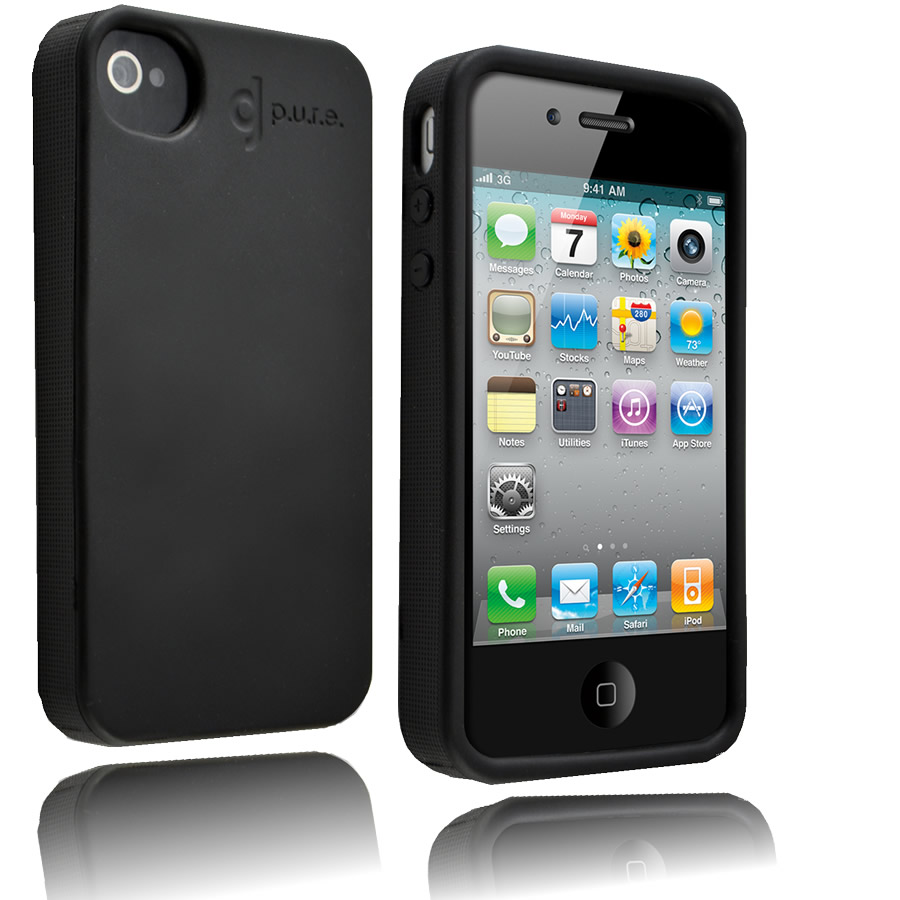
Flex
These rubber substitutes are known for their durability, pliability and strength
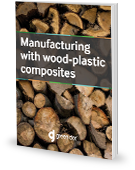
Manufacturing with wood-plastic composites
What product designers and plastics manufacturers need to know about working with wood-plastic composites
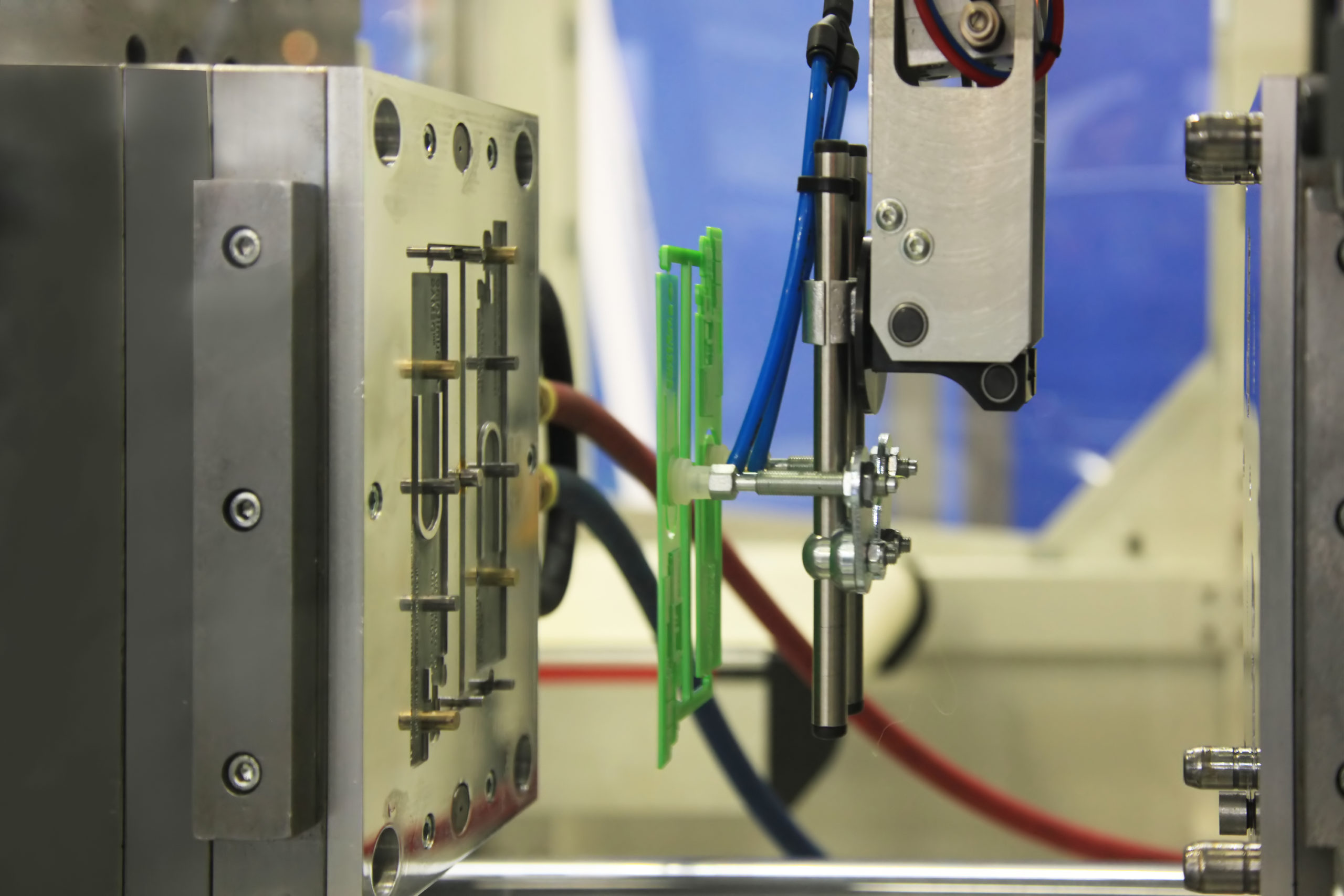
Injection molders who have made bioplastics work
Four injection molders share valuable and promising insights into what working with bioplastics entails.
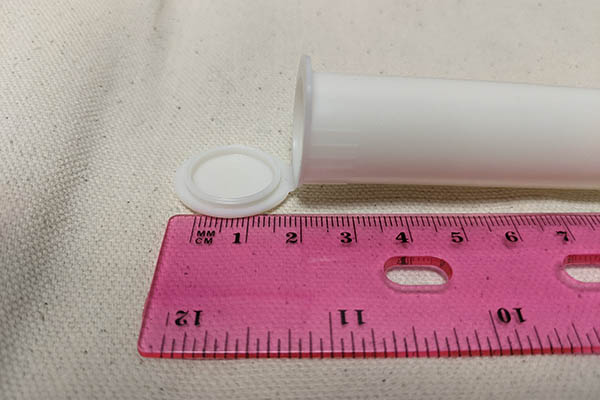
Green Dot Bioplastics achieves a compostable living hinge
Developing a solution to the living hinge challenge opens a lot of doors for sustainable packaging.
Frequently Asked Questions: Manufacturing with Bioplastics
Are you interested in manufacturing with bioplastics but wondering how the process differs from manufacturing with traditional plastics? We asked Mike Parker, Director of Research and Development at Green Dot Bioplastics, to explain the differences and similarities between bioplastics and traditional plastics, what special equipment is required to process bioplastics, and why the bioplastics manufacturing process is more sustainable than processing traditional plastics.
Q: What are the main differences between bioplastics and traditional plastics?
Mike: The core difference between bioplastics and traditional plastics is the feedstocks that are used to make the polymer and / or the end-of-life options for the polymer. Materials that use renewable, non-petroleum base feedstocks are referred to as biobased. Materials that break down when exposed to certain environments, like a compost pile, are considered compostable bioplastics. Using the word biodegradable as a generic reference can be problematic because it does not identify what environment is required. At Green Dot, all of our materials or their components have passed industrial composting standards. Both types are considered bioplastics. It is important to note that not all biobased materials are biodegradable and not all biodegradable materials are biobased. At Green Dot, we have two primary types of bioplastics: biocomposites which utilize traditional plastics like polypropylene (PP), polyethylene (PE), or nylon (PA) as the base material and are then blended with renewable plant-based fillers or fibers. These materials have biobased content but are not biodegradable. The other type of bioplastics we make are compostable plastics, which will biodegrade in a composting environment once the product reaches the end of its useful life. Another difference between bioplastics and traditional plastics is that bioplastics tend to be more hydroscopic than traditional plastics, meaning they can absorb moisture which results in the necessity of drying of the polymers prior to processing. Some traditional plastics need drying as well, such as nylon and bioplastics use the same drying process and equipment. Processing temperatures also tend to be lower for bioplastics due to either the plant-based content of the materials, which will burn if processed too hot, or the nature of the polymer. Bioplastics are still thermoplastic polymers and they process in a similar fashion to traditional materials through injection molding, profile extrusion, and film production.
Q: Do bioplastics require any additional or different equipment to process?
Mike: Bioplastics process on traditional plastics equipment.
Most people want to be able to use these materials in their existing tooling, rather than have to design a whole new tool. In many instances, this is achievable if we understand the shrink rate and melt flow rate that the tooling was designed for so that we can recommend a bioplastic option with similar properties for the greatest chance of success. Bioplastics can be more sensitive to heat and shear energy, so we typically try to avoid intense mixing or anything that would cause a high shear rate.
Q: You mentioned bioplastics are more sensitive to moisture. How does that affect the manufacturing process and finished parts?
Mike: This is where there’ll be a difference between compostable materials and biocomposites. A biocomposite is typically a combination of organic materials, such as fillers and fibers, and traditional plastics. It’s the fiber filler that draws the moisture in, so pre-drying is critical. If the moisture is not removed you will see things like nozzle drool, splay, and voids in injection molded parts. In an extrusion setting, you might see foaming or excessive off-gassing.
For compostable plastics moisture can cause a chemical reaction in the polymer called hydrolysis, which will make the material extremely fluid, increasing the melt flow rate drastically. Hydrolysis also causes part degradation and even a small amount can cause brittleness immediately or overtime reducing the shelf life of parts. It is critical to get the moisture content to 400 parts per million or less, before you process those materials. We highly recommend that anyone processing bioplastics have a moisture analyzer so they can properly measure the moisture content.
Q: How do the temperatures to process bioplastics differ from traditional plastics?
Mike: Most compostable polymers will process at roughly 300 to 380 degrees Fahrenheit and should not exceed 400 degrees. The same is true for biocomposites due to the plant-based fillers which will burn at 410 degrees. If thermal degradation occurs, dark streaks may be present, there may be off – gassing especially if the material was not dried properly, and there will likely be a burnt smell.
An advantage of processing at lower temperatures is less energy consumption. The lower the temperature, the less energy required for processing, which is another potential sustainability benefit of using bioplastics.
A thorough review of the technical datasheet will provide recommended processing parameters as well as drying instructions. We are also available for a pre-trial consultation to talk through any questions prior to a company sampling one of our materials.
Q: How does processing time and cycle times of bioplastics compare to traditional plastics?
Mike: Since bioplastics process at lower temperature, in some cases they have a shorter cooling time. Overall processing and cycle times are slightly longer than traditional plastics. With that said, materials from Green Dot do not require time for crystallization so they will have shorter cycle times than some types of PLA. We have projects where the switch to a bioplastic resin has reduced cycle times using existing tooling for existing parts which makes the compostable version more economical to manufacture.
Q: Thinking again about the equipment itself, what types of runner and gating systems can be used in injection molding applications?
Mike: We’ve run bioplastics in hot runner molds, as well as cold runner molds. Due to shear sensitivity, there are certainly parameters to watch when processing in a hot runner system but we have had good results using them. We’ve also had customers run them using various types of gates, including hot tip and valve gates, tab gates, fan gates, and tunnel gates. There are some materials that might be a little too stiff for some types of gates, but if we understand the system you are working with, we can provide material suggestions and processing parameters to alleviate some of these issues.
There are certainly exceptions, but in most cases, a completely new tooling set up is not necessary.
Q: In your testing, did any of these gating options prove to be more beneficial than the other? Or does it come down to the material itself?
Mike: It’s partly due to the material but primarily part design. Some parts fill better with a fan gate, some don’t. It’s more of a design and geometry question.
Q: What else should a manufacturer, OEM, or designer consider when designing or working with multi-cavity tools and bioplastics?
Mike: If we’re looking at biocomposite materials they will typically have a lower melt flow rate than a traditional plastic because of the filler content. In this case, larger gates and runners tend to help alleviate processing and flow issues. For compostable material, it’s usually less of a problem. They do typically have a little better melt flow rate and are easier to inject at lower pressures. Really the most important thing when you’re looking at designing tools, is thinking about shear heat. You’d want a hot runner system that was designed without much dead space, no 90-degree angles, anything that could create a disruption to the flow could potentially create shear. Aside from that, it’s similar to traditional plastics.
Q: Thinking about aesthetics, if I’m a designer or I’m an OEM and I would like to use bioplastics, what are my color options? Am I stuck with that kind of muddy color, the browns and greens that you can just see at a glance, ‘oh, this must be organic’?
Mike: Not at all. We’ve successfully colored both biocomposites as well as compostable materials ranging from pastels to safety orange. Any of the commercial color houses can match these materials and provide a masterbatch, liquid, or dry pigments in the same way traditional plastics are colored.
For biocomposites, your typical PP, PE, or EVA carrier resin will work just fine. Of note, once colored, the filler is still visible giving the finished product a natural aesthetic which most of our customers see as a critical marketing tool for product differentiation the consumer can see.
The critical difference is that when coloring a compostable polymer, the carrier resin also MUST be compostable and the pigments should meet the industry standards for compostability and heavy metals guidelines.
Q: Mike, any closing thoughts?
Mike: I want to stress that working with bioplastics, both biocomposites and compostable polymers, is not that different than making the change over from running a polypropylene to running ABS. The two materials are different. They have a different chemical make up, they have different temperature profiles, and the finished parts will have different physical attributes but they are both thermoplastics. The technical data sheet for any material, whether it is a bioplastic or traditional plastic will provide guidelines for processing and temperature. Be sure to review this with your processing team and operators. If you have questions, let us know. A quick 15 or 20 minute phone call to discuss the details and processing parameters can save a lot of time and increase the chances of first time success when running a new material in an existing tool.
Ready for Prime Time
Green Dot has biobased materials ready for your operation now, be a part of the transformation.
Contact Us