Terratek WC Wood-Plastic Composite
- WC100299 data sheet
- WC100300 data sheet
- WC200118 data sheet
- WC200180 data sheet
- WC200199 data sheet
- WC200300 data sheet
The Terratek® WC line of wood-plastic composites combines the pleasing look of wood with the functionality and manufacturing ease of plastics. These wood-plastic composites blend fine wood particles with renewable, biodegradable, reclaimed, recycled, or virgin plastic materials to make firm, smooth pellets for convenient handling and further processing.
The wood fibers are obtained from waste materials generated by lumber manufacturers, which are then processed to produce a consistent reinforcing product. The use of these particles promotes the reclamation of wood waste that would otherwise be sent to landfills and ensures that no new trees are cut down to make the product. Wood-plastic composites also reduce energy use, since they melt at lower temperatures than typical plastics.
Perhaps most recognizable as decking materials, wood-plastic composites in fact display an incredibly wide range of potential applications. By adjusting the species, size and concentration of wood particles in the formulation, different properties can be achieved. Wood-plastic composites can even be foamed to make a strong lightweight material.
Similarly, the chosen wood species will also have a bearing on the final product’s color. Pine fillers tend to produce products that are lighter in color compared to hardwood fillers. Larger wood particles will also have an effect on the finished look, giving the product a more natural appearance.
This variability in the look and feel of products made from wood-plastic composites opens these materials up to a wide range of designer preferences. Product applications have included children’s toys (since colors can be customized, there’s no need for potentially toxic paints), dog toys (even imitating the taste of Fido’s favorite, but more splintery, wooden sticks), automotive interiors, patio furniture, garden edging and more.
Wood-plastic composites are capable of achieving a huge range of characteristics while always keeping one thing in common: sustainability. As consumer attitudes towards our responsibility to the planet are changing, smarter materials offer a way forward.
More application examples
- Outdoor decking materials
- Fencing materials
- Siding
- Lawn and garden
- Furniture
- Toys
- Injection molded and profile extruded articles
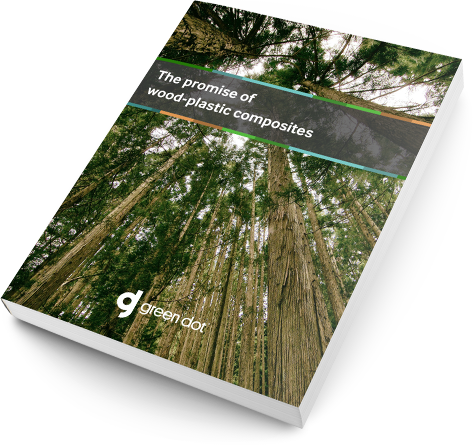
The promise of wood-plastic composites
Learn how plastics combined with reclaimed wood are emerging as a sustainable alternative to traditional plastics.
Working with wood-plastic composites
Terratek WC can contain up to 60 percent wood particles, significantly reducing dependence on petroleum-based plastic materials, while simultaneously promoting the use of recycled wood. Additionally, in many applications the plastic materials that are used can be obtained from post-industrial or post-consumer recycling sources, further reducing the need for more plastic resin derived directly from petroleum and increasing the use of reclaimed materials.
The Terratek WC 100300 formulation contains approximately 30 percent wood fibers and 70 percent reclaimed polypropylene. Terratek WC wood-plastic composites can be produced from a variety of wood particle types, including maple, oak and pine. Furthermore, they are available in an injection molding grade, as well as an extrusion grade.
Fortunately for manufacturers, processing wood-plastic composites is remarkably similar to processing traditional petroleum-based plastics. Large-scale investments in new tooling equipment are not required, as the material does not behave drastically differently.
It is helpful for manufacturers to know the exact formulation chosen by the product’s designers. Wood-plastic composites in general do tend to have lower melting temperatures, and care should be taken that they are not overheated.Wood-plastic composites generally process in temperatures around 50 degrees lower than the same, unfilled material. Most wood additives will begin to burn at around 400 degrees Fahrenheit. As a rule, the higher the ratio of wood to plastic, the lower the melting temperature.
An additional benefit wood particles lend to plastics during the production phase is one of dimensional stability. Because the wood particles structurally strengthen the product, they can be removed from the molding at a higher temperature than plastic alone. Over the long term, this can provide tremendous benefits in terms of shortening cycle time and improving productivity.
Once manufacturers are aware of the specific formulations chosen for a wood-plastic composite, the process of working with these materials is very similar to working with traditional plastics. There are even some benefits, beyond those of sustainability, which they bring to molding operations.
Advantages for manufacturers using wood-plastic composites from Green Dot
- Uniform pellet size for even melting
- Guaranteed low moisture content
- Lower processing temperatures
- Compatible with existing machinery
- Amenable to the addition of foaming agents
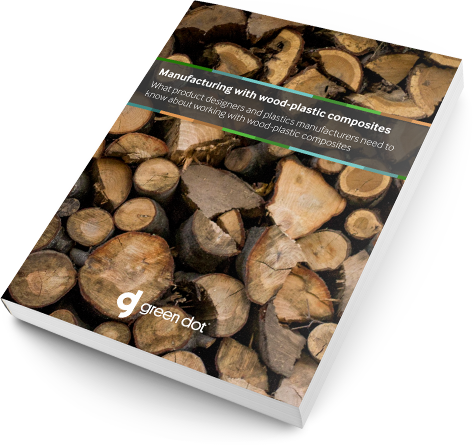
Working with wood-plastic composites
Why plastics manufacturers have nothing to fear by switching to a wood-plastic composite alternative material
Green Dot goes to great lengths to make sure manufacturing from its wood-plastic composites feels like familiar work for plastics molders. When that’s the case, designers can focus on all the additional benefits these materials bring to a product’s design. Besides being a more sustainable alternative to fully petroleum-based raw materials, wood-plastic composites bring numerous advantages to products.
Additional advantages
- Weather stability
- Long life
- Less maintenance
- No splinter
- More natural look and feel
- Ease of processing
Interested in discussing whether our wood-plastic composite is right for your product? We’d be interested in hearing from you. Get in touch with us today to schedule a material selection consultation.