Formula & tooling considerations for manufacturing with wood-plastic composites
Designing and manufacturing from a wood-plastic composites is a remarkably similar process to working with traditional plastics. There are some additional variables, though, that designers and manufacturers should be aware of when material is being selected for a product. For manufacturers, understanding the effects of different ratios and tooling configurations on the process will help ensure a smooth project from start to finish.
The ratio of wood to plastic in the chosen formula of a wood-plastic composite will have some effect on its behavior as it goes through the production process. The percentage of wood present in the composite will have an effect on the melt flow index (MFI), for example. As a rule, the more wood that is added to the composite, the lower the MFI.
The percentage of wood will also have a bearing on the strength and stiffness of the final product. Generally speaking, the more wood that’s added, the stiffer the product becomes. Wood can make up as much as 70 percent of the total wood-plastic composite, but the resulting stiffness comes at the expense of the ductility of the final product, to the point where it may even risk becoming brittle.
Higher concentrations of wood also shorten machine cycle times by adding an element of dimensional stability to the wood-plastic composite as it cools in the mold. This structural reinforcement allows the plastic to be removed at a higher temperature than a conventional plastic. At temperatures where conventional plastics are still too soft to be removed from their molds, composites made with wood can successfully be ejected.
If the product will be manufactured using existing tools, the gate size and general shape of the molding should factor into the discussion of optimal wood particle size. A smaller particle will likely better serve tooling with small gates and narrow extensions. If other factors have already led designers to settle on a larger wood particle size, then it may be beneficial to redesign the existing tooling accordingly. But, given the existing options for different particle sizes, this outcome should be completely avoidable.
In general, the tooling considerations when working with wood-plastic composites are more or less the same as when working with conventional plastics. Even when changes are necessary, they can often be made as modifications to existing tooling, rather than from-scratch reboots. This compatibility makes beginning to work with wood-plastic composites a relatively easy transition.
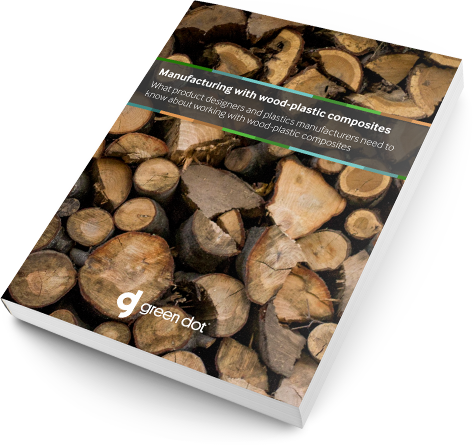
Working with wood-plastic composites
Why plastics manufacturers have nothing to fear by switching to a wood-plastic composite alternative material